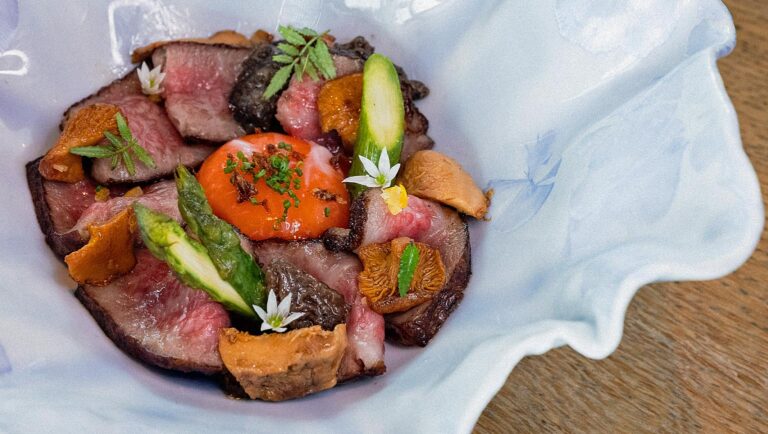
Review: Kokin – tuna meets fire at The Stratford
The new sushi restaurant now at the iconic skyscraper’s 7th floor and terrace
Porcelain Glass was conceived when Doug McMaster, of the world’s first zero-waste restaurant, Silo, asked me if there was a way of transforming the single-use glass being consumed at his restaurant into a new material. Pure silica is running out, so we need to find solutions to our glass packaging addiction. It’s time to exploit what we’re putting in our bins and start reclaiming, rather than just recycling. Recycling sometimes involves additives, which just postpones the problem. We can use glass as an aggregate, we can put it in our road surfacing, in our building materials, but ultimately we’re not solving a problem, just sweeping it, literally, under the carpet.
Making glass packaging is energy intensive so we need to explore that sacrifice and reuse, rather than discard that energy. Recycled glass usually requires a small percentage of new glass, whereas our process just uses the glass already available. We’re closing the loop completely and in that regard our approach is avantgarde. The ideal scenario is to have no single use glass. Unfortunately, I think we’re very far off from that, but we need to look at how we can utilise plastic, glass and other materials we’re putting in our bins. It’s a cost not only to the earth, but to the government. Currently, most of what we consume in the UK is exported to other countries, often ending up in a landfill anyway, just out of sight.
We’re doing the glass project in Malta too, where I’m originally from. The company is called Broken Bottle and we work with the government there, building a circular economy that creates new industry whilst keeping the material in-house. We reduce our carbon footprint this way and it saves us having to re-import or export waste glass to process it. The process we’ve come up with is less energy intensive too as we fire at a lesser temperature than in normal glass recycling.
Glass and clay have Silica in common so they’re not unrelated. Doug’s challenge gave me the opportunity to explore the material as a potter rather than a glassmaker. I probably crossed some boundaries which might be frowned upon from glassmakers. After a lot of trials, errors and tears we’ve come up with this wonderful material we’re calling glass porcelain. Even at this stage, we’re only scratching the surface of its potential. We’re finding ways to cold cast and also looking at how to get it back into glaze, so there are many other avenues to explore with this material we call waste, which I think is a really poor choice of words. We’re finding ways to service the community here by taking away domestic and industrial glass and turning it into porcelain glass. Winning the Vitra design award last year was a wonderful acknowledgement of the mission we’ve set out to do and we’re keen to work with anyone who’s interested in finding positive uses for this material.
I was lucky enough to grow up in a pottery. My mum was a potter and instrumental to the Maltese pottery scene. Back in the early ‘80s it was a very male-oriented trade, so she faced a lot of challenges to get the materials she needed and to teach people the craft. She identified my affinity with the practice at an early age. I’ve done many other jobs, but nothing gives me that satisfaction I get with pottery. As a practice, pottery is now proven as a therapy. It’s so absorbing that you don’t have the capacity to hold onto any other thoughts while you work with clay. You’re transported to this calm, positive place. Back at my old studio in Brighton, we worked with groups facing difficulties and the benefits there were very apparent. We’re going to continue with this here in Hackney Wick too. Personally, pottery has helped me get through some difficult times. It’s my way of dealing with things, whether that’s happiness, anger, sadness, it just grounds me and keeps me going. I don’t know if it’s the clay that brings you down to earth but all the potters I’ve met are positive people.
Phil Rogers is an important person in my pottery journey and in the contemporary ceramic scene generally. He came up with ash glazes, another zero-waste approach that turns the ashes from burnt down trees into glaze. Trees, like all plants, absorb minerals from the earth and once we get rid of the carbon we are left with those minerals. Different trees pull out different metals and silicates from the earth resulting in different effects. We’re keen to explore this at Silo, with homage to Rogers. At the restaurant everything is done on an open flame, which we call the ‘open heart’. The birch wood that’s used as fuel, and it’s resulting ashes can be used in the crockery we produce, closing another loop.
As an artist, I’m always on a learning curve. I’ve never reached a stage of being bored. There’s always a discovery to be made and the excitement of trying something for the first time. Waiting for the kiln to cool down is like Christmas Eve. The excitement is yet to fizzle out. Pottery is like a corridor of doors and every time you open one there’s another corridor. This is one of the oldest technologies in the world, the first after fire, and it is still giving. We make insulation for space crafts out of clay, we make performance engine blocks and brake discs. It never reaches a point of saturation and that’s what I find so fascinating. There are always new things to discover, like glass porcelain.
Pottery, like life, has taught me patience. The pandemic forced us to come to terms with the things we cannot control. Watching my business slip away and loved ones pass, all these different horrible things I couldn’t have imagined happening, showed me that all I could do was worry about the things I can change. Pottery really helps me with that, too.
Find out more including details of pottery classes at: pottersthumb.com
The new sushi restaurant now at the iconic skyscraper’s 7th floor and terrace
Exploring the health advantages of belonging to something bigger than ourselves
Your timely reminder to go visit these amazing restaurants, bars and cafes this summer while we wait for better bridge access…
A joint venture in collaborative local media from:
In partnership with
Regulated by IMRESSS, the Independent Monitor for the Press CIC.
For more info on our complaints policy, or to make a complaint, visit FAQ.